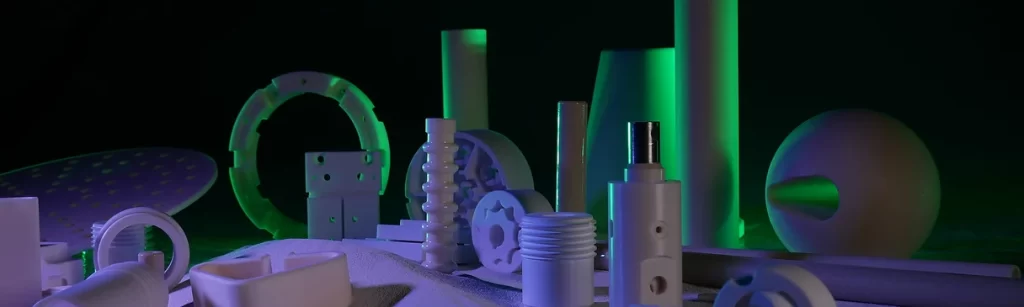
Custom Technical Ceramic Manufacturing
International Ceramic Engineering specializes in the design and manufacture of custom advanced ceramic components and performance plastic components. The demand for high-performance materials in various industries has led to the development and adoption of advanced ceramics. Custom Technical Ceramics Manufacturing involves the design, production, and optimization of ceramic components tailored to specific applications and requirements. This white paper explores the features, benefits, and applications of custom ceramic manufacturing, highlighting its importance in modern industry.
Performance plastics offer superior performance and reliability, making them an ideal choice for ceramic parts manufacturing.
We provide the following advanced ceramic and performance plastic machining services:
- Hard Grinding of Ceramics
- Extruded Ceramics
- Pressed Ceramics
- Cast Ceramics
- Powder Processing
- Green Machining
- Extrusion
- Iso-Pressing
- Dry Pressing
- Casting
- Sintering
- Wet Grinding
- Outside Diameter Machining
- Inside Diameter Machining
- Surface Grinding
- Ultra Sonic Holes
- Ultra Sonic Milling
- Cones & Tapers
- Spherical Radius Grinding
- Finest Blade and Edge Sharpness
- Tapping Services
- Honing Services
- Angle Grinding
International Ceramic Engineering can also clean, flame polish, glaze, tumble, anneal and heal fire your advanced ceramic components.
What is Custom Technical Ceramics Manufacturing?
Custom Technical Ceramics Manufacturing is the process of creating ceramic components designed to meet specific technical requirements. This involves selecting the appropriate ceramic materials, utilizing advanced manufacturing techniques, and tailoring the properties and shapes of the ceramics to suit particular applications. The process can include green machining, sintering, and post-sintering operations to achieve the desired specifications.
Features of Custom Technical Ceramics Manufacturing
1. Material Selection
- Diverse Material Options: A wide range of ceramic materials, including alumina, zirconia, silicon carbide, and silicon nitride, can be selected based on their unique properties such as hardness, thermal resistance, and electrical insulation.
- Tailored Properties: Custom ceramic manufacturing allows for the adjustment of material properties to meet specific performance criteria, such as enhanced strength, improved wear resistance, or higher thermal stability.
2. Precision Manufacturing
- Advanced Techniques: Techniques such as green machining, hot pressing, and injection molding enable the production of complex shapes and fine details with high precision.
- Tight Tolerances: The use of high-precision equipment and processes ensures that custom ceramic components meet stringent dimensional and performance specifications.
3. Design Flexibility
- Complex Geometries: Custom ceramic manufacturing allows for the creation of intricate shapes and complex geometries that are difficult or impossible to achieve with traditional manufacturing methods.
- Prototyping and Iteration: The ability to quickly produce prototypes and iterate designs facilitates innovation and rapid development of new ceramic components.
Benefits of Custom Technical Ceramics Manufacturing
1. Performance Optimization
- Enhanced Properties: Custom ceramics can be engineered to exhibit superior mechanical, thermal, and electrical properties, tailored to specific applications.
- Reliability and Durability: High-quality custom ceramics offer excellent reliability and longevity, reducing the need for frequent replacements and maintenance.
2. Cost Efficiency
- Material Efficiency: Custom manufacturing processes minimize material waste, optimizing the use of expensive ceramic materials.
- Reduced Tooling Costs: Precision manufacturing techniques reduce wear on tools and equipment, lowering operational costs over time.
3. Application-Specific Solutions
- Tailored Components: Custom ceramic manufacturing allows for the production of components designed to meet the exact needs of specific applications, enhancing performance and efficiency.
- Industry-Specific Solutions: Whether for aerospace, medical, electronics, or industrial applications, custom ceramics provide solutions that meet the unique challenges of each industry.
4. Environmental Sustainability
- Reduced Waste: Efficient manufacturing processes and precision machining reduce material waste, contributing to more sustainable production practices.
- Energy Efficiency: Advanced manufacturing techniques often require less energy than traditional methods, reducing the environmental impact of production.
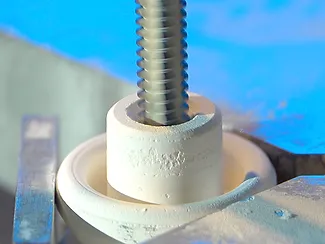
Technical Processes in Custom Ceramic Manufacturing
1. Green Machining
- Pre-Sintered State: Machining ceramics in their pre-sintered, or green, state allows for easier shaping and higher precision.
- Tooling and Techniques: Specialized tools and techniques are used to achieve complex shapes and tight tolerances.
2. Sintering
- Densification: Sintering involves heating the ceramic material to a high temperature to achieve densification and enhance mechanical properties.
- Controlled Atmospheres: The process can be carried out in controlled atmospheres to prevent contamination and achieve the desired material properties.
3. Post-Sintering Operations
- Grinding and Polishing: Post-sintering operations such as grinding and polishing are used to achieve the final dimensions and surface finish of the ceramic components.
- Coating and Finishing: Additional coatings and surface treatments can be applied to enhance the performance and durability of the ceramic parts.
Custom Technical Ceramics Manufacturing offers a versatile and efficient approach to producing high-performance ceramic components tailored to specific applications. With its ability to optimize material properties, enhance precision, and provide application-specific solutions, custom ceramic manufacturing is a critical process in modern industry. As technology advances, the capabilities and applications of custom ceramics will continue to expand, driving innovation and improving performance across various sectors.
Custom Technical Ceramics Manufacturing offers tailored solutions that meet the specific needs of various industries. By leveraging the unique properties of advanced ceramics and utilizing precision manufacturing techniques, custom ceramic components provide superior performance, durability, and efficiency in a wide range of applications. As technology continues to advance, the capabilities and applications of custom ceramics will expand, driving innovation and improving performance across multiple sectors. Call or email International Ceramic Engineering to discuss your specific needs or use our contact form.
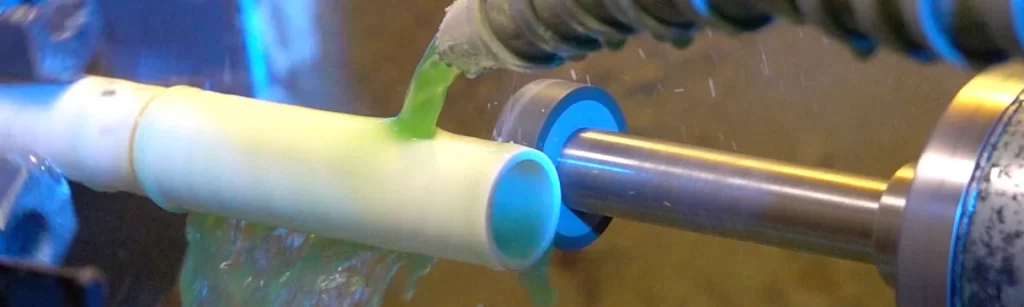
International Ceramic Engineering provides cutting-edge ceramic parts manufacturing and machining services. We specialize in machining components before sintering, to ensure superior accuracy and performance, and to save money. (MACHINING IT GREEN).
Why? Ceramics are harder than tool steel, so grinding and machining a hardened part takes a lot of time and tool wear.
By machining the parts in the pre-hardened state, we can easily add features and dimensions in a tenth of the time. In fact we can add features to your parts that can’t be made any other way.
This method of ceramic manufacturing allows us to create and deliver high-quality, high-precision parts in custom geometries. Our machining process reduces the amount of time and effort needed to achieve the desired precision, making it the most efficient option for ceramic parts manufacturing.
But if you need diamond grinding…
International Ceramic Engineering is an expert at diamond grinding of advanced ceramic materials.
Diamond grinding is a process used to shape and finish ceramic parts. It involves the use of abrasive diamond particles bonded to a wheel that rotates at high speeds to grind away material from the surface of the ceramic part. The diamond grinding process yields a high-precision finish that is uniform and smooth. This process can be used to machine complex shapes and profiles with excellent accuracy and repeatability.
Also …advanced performance plastics
Performance plastics are a class of polymers that offer enhanced properties over traditional plastics, such as superior strength, chemical resistance, and heat resistance. They are used in ceramic parts manufacturing to produce components with superior durability, strength, and flexibility.
Performance plastics are ideal for components that need to withstand extreme temperatures and harsh environments. They are also able to maintain their shape and integrity under intense stress, making them ideal for applications that require precision and accuracy.
Common types of performance plastics used in ceramic parts manufacturing include Polyphenylene Sulfide (PPS), Polyether Ether Ketone (PEEK), Polyetherimide (PEI), Polytetrafluoroethylene (PTFE), and Polychlorotrifluoroethylene (PCTFE).