What is Green Machining Ceramics?
International Ceramic Engineering provides cutting-edge ceramic parts manufacturing and machining services. We specialize in machining components before sintering, to ensure superior accuracy and performance, and to save money. (MACHINING IT GREEN).
Why? Ceramics are harder than tool steel, so grinding and machining a hardened part takes a lot of time and tool wear.
By machining the parts in the pre-hardened state, we can easily add features and dimensions in a tenth of the time. In fact we can add features to your parts that can’t be made any other way.
This method of ceramic manufacturing allows us to create and deliver high-quality, high-precision parts in custom geometries. Our machining process reduces the amount of time and effort needed to achieve the desired precision, making it the most efficient option for ceramic parts manufacturing.
Green machining ceramics refers to the process of shaping ceramic materials while they are in a pre-sintered, or “green,” state. This involves the use of specialized tools and techniques to machine the ceramic material before it undergoes the final sintering process, where it is heated to achieve its final properties.
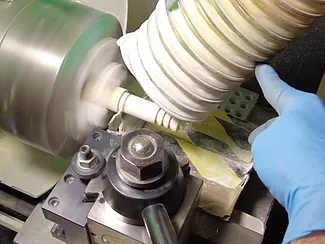
Features of Green Machining Ceramics
1. Material State
- Pre-sintered Condition: The ceramics are machined while in a green state, making them softer and easier to shape compared to their fully sintered counterparts.
- Consistency: The green state ensures uniformity in the material, which is critical for achieving precise dimensions and shapes.
2. Tooling and Equipment
- Specialized Tools: Green machining requires specific tools designed to handle the delicate nature of pre-sintered ceramics.
- Precision Machinery: High-precision machining equipment is used to ensure accuracy and repeatability in the machining process.
3. Flexibility in Design
- Complex Geometries: The green state allows for the creation of complex shapes and intricate designs that would be challenging or impossible to achieve with fully sintered ceramics.
- Customization: Manufacturers can easily modify designs and prototypes, making green machining ideal for custom and low-volume production runs.
Benefits
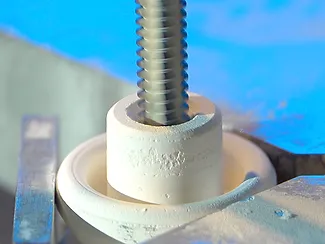
Benefits
- 1. Cost Efficiency
- Reduced Tool Wear: Machining ceramics in their green state significantly reduces wear and tear on cutting tools, leading to lower tooling costs.
- Lower Energy Consumption: The machining process requires less energy compared to post-sintering machining, contributing to overall cost savings.
2. Enhanced Precision
- Dimensional Accuracy: Green machining allows for tight tolerances and high precision, ensuring that the final product meets exact specifications.
- Reduced Material Waste: The ability to machine ceramics in their green state minimizes material waste, as there is less need for rework or adjustments.
3. Environmental Sustainability
- Energy Efficiency: The lower energy requirements of green machining contribute to a smaller carbon footprint.
- Reduced Emissions: The process generates fewer emissions compared to traditional machining methods, aligning with environmental regulations and sustainability goals.
4. Improved Product Quality
- Consistency and Uniformity: The pre-sintered state of the ceramics ensures uniform material properties, leading to consistent and high-quality end products.
- Enhanced Mechanical Properties: Green machining can improve the mechanical properties of the final ceramic components, including strength and durability.
5. Shorter Lead Times
- Faster Production: The ease of machining in the green state accelerates the manufacturing process, resulting in shorter lead times for product delivery.
- Rapid Prototyping: Green machining is ideal for rapid prototyping, allowing for quick iteration and development of new ceramic products.
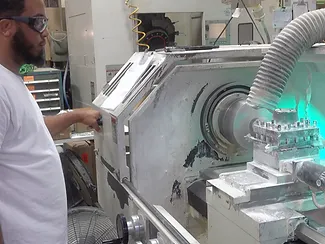
Applications
Applications of Green Machining Ceramics
Green machining ceramics has broad applications across various industries due to its ability to produce high-precision, durable, and complex ceramic components. Here, we delve deeper into the specific applications and benefits of green machining ceramics in different sectors.
1. Aerospace Industry
High-Temperature Components
- Turbine Blades: Turbine blades in jet engines and power generation turbines are often subjected to extreme temperatures and stresses. Green machining allows for the precise shaping of these blades from advanced ceramic materials, ensuring they can withstand high temperatures without deforming or degrading.
Thermal Protection Systems
- Heat Shields: Ceramic heat shields protect spacecraft from the intense heat generated during re-entry into the Earth’s atmosphere. The precision and customizability of green machining make it possible to produce complex shapes that fit the unique contours of each spacecraft.
2. Medical Industry
Surgical Instruments and Implants
- Bone Implants: Ceramics are biocompatible and often used in medical implants such as hip and knee replacements. Green machining enables the production of custom-fitted implants tailored to the patient’s anatomy, improving the success rates of surgeries.
- Dental Crowns and Bridges: The ability to machine ceramics with high precision ensures that dental restorations fit perfectly, providing durability and aesthetics.
Diagnostic Equipment
- MRI Components: Ceramic components are used in MRI machines due to their non-magnetic properties. Green machining ensures these components meet the strict dimensional and material requirements necessary for accurate medical imaging.
3. Electronics Industry
Substrates and Insulators
- Microelectronic Substrates: Ceramics are widely used as substrates in microelectronic devices due to their excellent thermal and electrical insulating properties. Green machining allows for the production of substrates with precise dimensions and complex patterns, essential for high-performance electronics.
- Capacitors and Resistors: Ceramic materials are crucial in the manufacture of capacitors and resistors. Green machining provides the precision required to produce these components at high tolerances, ensuring consistent electrical performance.
Sensors and Actuators
- Piezoelectric Devices: Ceramics with piezoelectric properties are used in sensors and actuators. Green machining facilitates the production of these devices with intricate geometries, enhancing their sensitivity and functionality.
4. Automotive Industry
Engine Components
- Combustion Chamber Liners: Ceramic liners in combustion chambers help withstand high temperatures and reduce wear. Green machining ensures these components are produced with the necessary precision and durability.
- Spark Plug Insulators: Ceramics are used in spark plug insulators due to their high dielectric strength. The precision of green machining ensures optimal performance and longevity of the spark plugs.
Emission Control
- Catalytic Converter Substrates: Ceramics are essential in catalytic converters for reducing vehicle emissions. Green machining allows for the production of honeycomb structures that maximize surface area for catalytic reactions, improving the efficiency of emission control systems.
5. Industrial Applications
Cutting Tools and Abrasives
- Machining Tools: Ceramic cutting tools and abrasives are valued for their hardness and wear resistance. Green machining allows for the production of tools with precise cutting edges and complex geometries, enhancing their performance in industrial machining operations.
- Grinding Wheels: High-precision green machining techniques ensure grinding wheels have the exact shape and surface characteristics needed for efficient material removal.
Chemical Processing
- Wear-Resistant Components: Ceramics are used in chemical processing equipment due to their resistance to corrosion and wear. Green machining produces components such as valves, seals, and nozzles that maintain their integrity in harsh chemical environments.
6. Energy Sector
Renewable Energy Systems
- Fuel Cells: Ceramic materials are used in solid oxide fuel cells (SOFCs) for their ionic conductivity and stability at high temperatures. Green machining allows for the precise fabrication of components that are critical to the efficiency and longevity of fuel cells.
- Solar Panels: Advanced ceramics are used in certain components of solar panels. The precision of green machining ensures that these components contribute to the overall efficiency and durability of solar energy systems.
7. Telecommunications
High-Frequency Components
- Ceramic Filters and Resonators: Ceramics are used in telecommunications for filters and resonators that operate at high frequencies. Green machining allows for the production of these components with the exact dimensions and properties required for optimal performance.
The applications of green machining ceramics are vast and varied, touching nearly every aspect of modern technology and industry. By leveraging the unique properties of ceramics and the precision of green machining, manufacturers can produce high-quality, durable, and complex components that meet the demands of diverse applications. As technology continues to advance, the role of green machining ceramics in driving innovation and sustainability will only grow, solidifying its importance in the future of manufacturing.
Benefits of Green Machining Ceramics
Green machining ceramics offers numerous advantages over traditional machining processes, making it an attractive option for manufacturers seeking efficiency, precision, and sustainability. Below are the key benefits in detail:
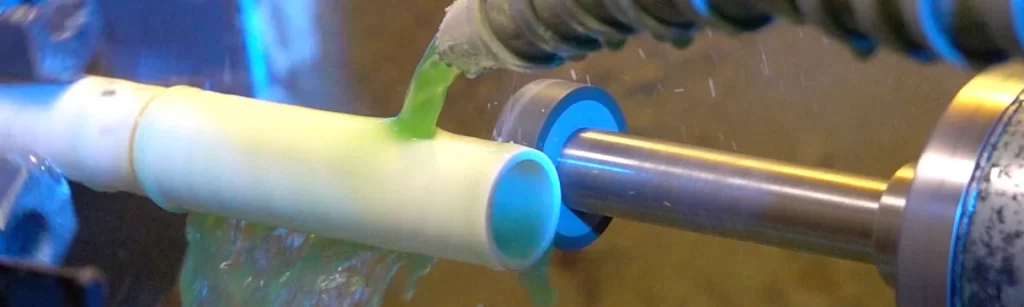
1. Cost Efficiency
Reduced Tool Wear
- Longevity of Tools: Machining ceramics in their green state, when they are softer, significantly reduces wear and tear on cutting tools. This extends the lifespan of the tools and lowers the frequency of replacements, leading to substantial cost savings over time.
- Lower Tooling Costs: Since green ceramics are easier to machine, the initial investment in tooling can be lower compared to machining fully sintered ceramics, which require more robust and expensive tools.
Lower Energy Consumption
- Efficient Machining: The green machining process requires less energy compared to post-sintering machining, as the material is softer and easier to cut. This results in lower energy bills and a reduced carbon footprint.
- Streamlined Production: The efficiency of green machining contributes to faster production times, reducing labor costs and increasing overall productivity.
2. Enhanced Precision
Dimensional Accuracy
- Tight Tolerances: Green machining allows for the achievement of tight tolerances, ensuring that the final product meets exact specifications. This is crucial in industries where precision is paramount, such as aerospace and medical devices.
- Consistency: The uniformity of the green state ensures that each machined part maintains consistent dimensions and properties, leading to higher quality and reliability.
Reduced Material Waste
- Efficient Material Use: The ability to machine ceramics precisely in their green state minimizes material waste. This is particularly important for expensive ceramic materials, where reducing scrap can lead to significant cost savings.
- Reduced Rework: High precision in the green machining stage means less rework or adjustments are needed post-sintering, streamlining the manufacturing process and reducing waste.
3. Environmental Sustainability
Energy Efficiency
- Lower Carbon Footprint: The reduced energy requirements of green machining contribute to a smaller carbon footprint. This aligns with global efforts to reduce greenhouse gas emissions and promote sustainable manufacturing practices.
- Resource Conservation: Efficient use of materials and energy in green machining conserves natural resources, supporting environmental sustainability.
Reduced Emissions
- Cleaner Process: Green machining generates fewer emissions compared to traditional machining methods. This not only benefits the environment but also helps manufacturers comply with stringent environmental regulations.
- Sustainable Manufacturing: By adopting green machining practices, companies can enhance their reputation as environmentally responsible organizations, appealing to eco-conscious consumers and stakeholders.
4. Improved Product Quality
Consistency and Uniformity
- Uniform Properties: Machining ceramics in their green state ensures uniform material properties, leading to consistent and high-quality end products. This is critical in applications where reliability and performance are essential.
- Homogeneous Material: The pre-sintered state of ceramics allows for a more homogeneous material, which contributes to the overall strength and durability of the final product.
Enhanced Mechanical Properties
- Strength and Durability: Green machining can improve the mechanical properties of ceramic components, such as strength and durability. This makes them suitable for demanding applications where high performance is required.
- Surface Finish: The precision of green machining results in smoother surface finishes, which can enhance the aesthetic and functional properties of the final product.
5. Shorter Lead Times
Faster Production
- Accelerated Machining: The ease of machining in the green state accelerates the manufacturing process, resulting in shorter lead times for product delivery. This is particularly beneficial in industries where time-to-market is critical.
- Efficient Workflow: Streamlined machining processes reduce bottlenecks and improve workflow efficiency, allowing manufacturers to meet tight deadlines and respond quickly to market demands.
Rapid Prototyping
- Quick Iteration: Green machining is ideal for rapid prototyping, allowing for quick iteration and development of new ceramic products. This enables manufacturers to innovate and refine designs more quickly and efficiently.
- Customization: The flexibility of green machining allows for easy modifications and customization of prototypes, facilitating the development of tailored solutions to meet specific customer requirements.
6. Flexibility in Design
Complex Geometries
- Intricate Shapes: The green state of ceramics allows for the creation of complex shapes and intricate designs that would be challenging or impossible to achieve with fully sintered ceramics. This opens up new possibilities for innovative product designs.
- Design Freedom: Manufacturers can explore a wider range of design options and push the boundaries of what is possible with ceramic materials.
Customization
- Tailored Solutions: Green machining enables the production of custom-fitted components, meeting the unique needs of various applications. This is particularly valuable in industries such as medical devices, where bespoke solutions are often required.
- Adaptability: The ability to easily modify designs and prototypes makes green machining suitable for both low-volume and high-volume production runs, providing flexibility to manufacturers.
The benefits of green machining ceramics are manifold, making it an increasingly popular choice in modern manufacturing. Its cost efficiency, enhanced precision, environmental sustainability, improved product quality, shorter lead times, and design flexibility offer compelling advantages over traditional machining methods. By adopting green machining practices, manufacturers can achieve higher quality products, reduce costs, and contribute to a more sustainable future. As technology continues to advance, the role of green machining ceramics in driving innovation and efficiency will only grow, solidifying its importance in the manufacturing landscape.
Cost Efficiency in Green Machining Ceramics
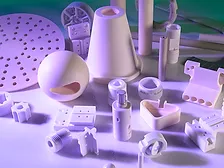
Cost Efficiency
Cost efficiency is one of the most significant advantages of green machining ceramics. This section delves deeper into the various aspects of cost savings achieved through this advanced manufacturing process.
Reduced Tool Wear
Longevity of Tools
- Tool Durability: Green machining involves working with ceramics in their pre-sintered, softer state. This reduced hardness means that cutting tools experience less abrasion and wear, extending their operational life. As a result, manufacturers face lower tooling replacement costs.
- Decreased Maintenance: With reduced wear, the need for frequent tool maintenance and sharpening diminishes. This not only saves on maintenance costs but also minimizes downtime, keeping production lines running smoothly.
Lower Tooling Costs
- Initial Investment: The tools required for green machining are typically less robust and expensive than those needed for machining fully sintered ceramics. This leads to lower initial tooling investment.
- Reduced Consumable Costs: As tools last longer and require less frequent replacement, the ongoing costs associated with consumables decrease significantly.
Lower Energy Consumption
Efficient Machining
- Energy Savings: Machining pre-sintered ceramics requires less force and energy compared to machining fully sintered ceramics. This results in lower electricity consumption and reduced operational costs.
- Optimized Processes: The efficiency of green machining processes can lead to shorter machining cycles, further reducing energy consumption per part produced.
Streamlined Production
- Faster Processing: The ease with which green ceramics can be machined speeds up the production process. Faster machining times translate to higher throughput and lower labor costs per unit.
- Reduced Machine Wear: Machines experience less stress and wear when machining softer, green-state ceramics. This can extend the life of the machining equipment, reducing long-term capital expenditure on machinery.
Material Savings
Reduced Material Waste
- Precision Machining: The high precision achievable with green machining minimizes material waste. Accurate initial machining means fewer errors and less scrap material, leading to cost savings in raw materials.
- Efficient Material Use: The ability to machine complex shapes and fine details in the green state reduces the need for additional material processing or adjustments after sintering.
Reduced Rework
- Fewer Defects: The precision of green machining significantly lowers the defect rate. With fewer parts needing rework or rejection, manufacturers save on labor and materials costs associated with correcting defects.
- First-Time Quality: Achieving the desired specifications in the first machining attempt minimizes the need for additional cycles of machining and inspection, streamlining the production process and saving costs.
Labor and Production Costs
Increased Productivity
- Higher Throughput: The efficiency of green machining allows for faster production rates, enabling manufacturers to produce more parts in less time. This increases overall productivity and reduces the labor cost per unit.
- Reduced Overtime: Faster production times and higher precision mean fewer instances of overtime required to meet production targets, leading to labor cost savings.
Simplified Processes
- Less Complex Setup: The reduced hardness of green ceramics simplifies the machining setup process, lowering the time and labor required for machine preparation and adjustments.
- Integrated Workflow: Green machining can be seamlessly integrated into existing production workflows, minimizing the need for extensive retraining or process overhauls.
Sintering Efficiency
Optimized Sintering Process
- Uniform Material Properties: Green machining ensures uniform material properties, which can lead to more predictable and efficient sintering cycles. This reduces energy consumption during sintering and minimizes the risk of defects that require costly re-sintering.
- Batch Consistency: Consistent machining in the green state results in uniform batches of parts, allowing for more efficient and effective sintering processes.
Investment in Innovation
Lower R&D Costs
- Prototyping Efficiency: Green machining is ideal for rapid prototyping, enabling manufacturers to quickly iterate and refine designs. This accelerates the development cycle and reduces the costs associated with lengthy R&D phases.
- Flexibility in Design Changes: The ability to easily modify designs and prototypes without significant cost implications encourages innovation and reduces the financial risk associated with product development.
The cost efficiency of green machining ceramics is multifaceted, encompassing reduced tool wear, lower energy consumption, material savings, labor and production cost reductions, and optimized sintering processes. By adopting green machining practices, manufacturers can achieve significant cost savings while maintaining high standards of precision and quality. This positions green machining ceramics as a financially viable and competitive option in the modern manufacturing landscape.
Starting with a thought exchange allows us to create and deliver high-quality, high-precision parts in custom geometries to meet your expectations because you have a better understanding of the process and outcome.
Start now by CALLING 800-779-3321